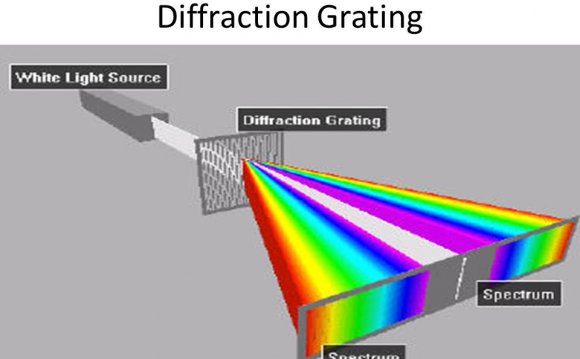
A fiber Bragg grating comprises many reflection points that reflect particular wavelengths of incident light. Such a point is created by intense UV light affecting the fiber core. This process is also called " are transmitted through the grating without being reflected or damped. Interference of the light of the individual reflection peaks creates a reflection peak determined by the distance of the grating points from each other.

If all reflections are in phase - in this case the wavelength corresponds to the distance of the reflection points -, this results in constructive interference at this point. The wavelength of such a reflection peak is determined in the interrogator. As soon as a fiber Bragg grating is subjected to strain, the distance of the reflection points changes and a different wavelength is reflected. This enables the Bragg wavelength variation to be determined. In analogy to the relationship for the metal strain gage, the following applies:
With
λ base wavelength of the fiber Bragg grating (wavelength at the start of measurement)
Δλ wavelength variation sith strain applied to the grating
k gage factor
ε strain
Fiber Bragg sensors have a higher layer thickness than electrical strain gages. When measuring bending strain of thin components, this results in a measurement error that must not be neglected but is easy to compensate for:
With
εOF strain on the component's surface
εAnz strain measured by the fiber